Lorsqu'on leur demande à quoi ils envisagent ce à quoi pourraient ressembler les robots, la plupart des gens pensent à de gros robots imposants travaillant dans des zones clôturées de grandes usines, ou à des guerriers blindés futuristes qui imitent le comportement humain.
Entre-temps, cependant, un nouveau phénomène apparaît discrètement : l'émergence de ce que l'on appelle les « cobots », qui peuvent travailler directement aux côtés d'employés humains sans avoir besoin de barrières de sécurité pour les isoler.Nous espérons que ce type de cobot pourra combler le fossé entre les chaînes d’assemblage entièrement manuelles et celles entièrement automatisées.Jusqu’à présent, certaines entreprises, en particulier les PME, pensent encore que l’automatisation robotique est trop coûteuse et compliquée et n’envisagent donc jamais la possibilité de l’appliquer.
Les robots industriels traditionnels sont généralement volumineux, fonctionnent derrière des écrans de verre et sont largement utilisés dans l'industrie automobile et d'autres grandes chaînes d'assemblage.En revanche, les cobots sont légers, très flexibles, mobiles et peuvent être reprogrammés pour résoudre de nouvelles tâches, aidant ainsi les entreprises à s'adapter à une production d'usinage plus avancée à faible volume pour relever les défis de la production en petites séries.Aux États-Unis, le nombre de robots utilisés dans l’industrie automobile représente encore environ 65 % des ventes totales du marché.L'American Robot Industry Association (RIA), citant des données d'observateurs, estime que parmi les entreprises susceptibles de bénéficier des robots, seules 10 % des entreprises ont installé des robots jusqu'à présent.
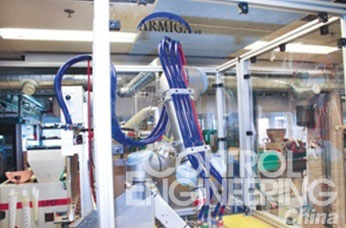
Le fabricant d'aides auditives Odicon utilise des bras robotisés UR5 pour effectuer diverses tâches dans la fonderie, tandis que les outils d'aspiration ont été remplacés par des pinces pneumatiques capables de gérer des pièces moulées plus complexes.Le robot à six axes a un cycle de quatre à sept secondes et peut effectuer des opérations de retournement et d'inclinaison qui ne sont pas possibles avec les robots Odicon conventionnels à deux et trois axes.
Manipulation précise
Les robots traditionnels utilisés par Audi n'ont pas pu résoudre les problèmes liés à l'applicabilité et à la portabilité.Mais avec les nouveaux robots, tout cela disparaît.Les composants des aides auditives modernes sont de plus en plus petits, mesurant souvent seulement un millimètre.Les fabricants d’aides auditives recherchaient une solution capable d’aspirer de petites pièces hors des moules.C'est totalement impossible à faire manuellement.De même, les "vieux" robots à deux ou trois axes, qui ne peuvent se déplacer que horizontalement et verticalement, ne peuvent pas être réalisés.Si, par exemple, une petite pièce reste coincée dans un moule, le robot doit pouvoir la retourner.
En une seule journée, Audicon a installé des robots dans son atelier de moulage pour de nouvelles tâches.Le nouveau robot peut être monté en toute sécurité sur le moule d'une machine de moulage par injection, aspirant les composants en plastique via un système de vide spécialement conçu, tandis que les pièces moulées plus complexes sont manipulées à l'aide de pinces pneumatiques.Grâce à sa conception à six axes, le nouveau robot est très maniable et peut retirer rapidement les pièces du moule par rotation ou inclinaison.Les nouveaux robots ont un cycle de travail de quatre à sept secondes, en fonction de la taille de la production et de la taille des composants.Grâce au processus de production optimisé, le délai d’amortissement n’est que de 60 jours.
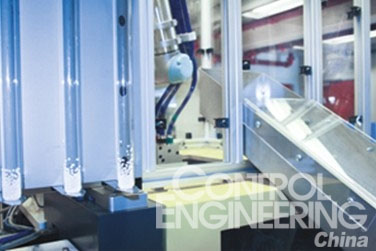
À l'usine Audi, le robot UR est solidement monté sur une machine de moulage par injection et peut se déplacer sur les moules et saisir les composants en plastique.Cela se fait à l'aide d'un système de vide spécialement conçu pour garantir que les composants sensibles ne sont pas endommagés.
Peut fonctionner dans un espace limité
Dans l'usine italienne Cascina Italia, un robot collaboratif travaillant sur une ligne de conditionnement peut traiter 15 000 œufs par heure.Equipé de pinces pneumatiques, le robot peut réaliser l’opération de conditionnement de 10 cartons d’œufs.Le travail nécessite une manipulation très précise et un placement minutieux, car chaque boîte à œufs contient 9 couches de 10 plateaux à œufs.
Au départ, Cascina ne s'attendait pas à utiliser des robots pour effectuer le travail, mais l'entreprise d'œufs a rapidement réalisé les avantages de l'utilisation des robots après les avoir vus en action dans sa propre usine.Quatre-vingt-dix jours plus tard, les nouveaux robots travaillent sur les lignes d'usine.Pesant seulement 11 livres, le robot peut se déplacer facilement d'une ligne de conditionnement à une autre, ce qui est crucial pour Cascina, qui possède quatre tailles différentes d'ovoproduits et a besoin que le robot puisse travailler dans un espace très limité à côté d'employés humains.
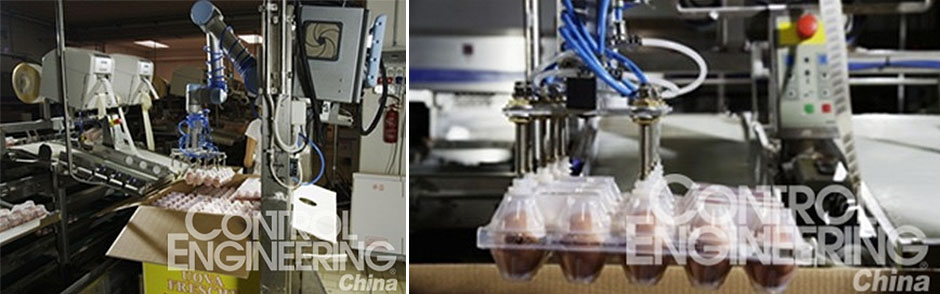
Cascina Italia utilise le robot UR5 d'UAO Robotics pour traiter 15 000 œufs par heure sur sa ligne de conditionnement automatisée.Les employés de l'entreprise peuvent rapidement reprogrammer le robot et travailler à côté sans utiliser de barrière de sécurité.Étant donné que l'usine de Cascina n'était pas prévue pour abriter une seule unité d'automatisation robotisée, un robot portable capable de se déplacer rapidement entre les tâches était crucial pour le distributeur d'œufs italien.
La sécurité d'abord
Pendant longtemps, la sécurité a été le point chaud et le principal moteur de la recherche et du développement des laboratoires robotiques.Compte tenu de la sécurité du travail avec les humains, la nouvelle génération de robots industriels se compose de joints sphériques, de moteurs à entraînement inverse, de capteurs de force et de matériaux plus légers.
Les robots de l'usine de Cascina répondent aux exigences de sécurité en vigueur en matière de limites de force et de couple.Lorsqu’ils entrent en contact avec des employés humains, les robots sont équipés de dispositifs de contrôle de force qui limitent la force de contact pour éviter les blessures.Dans la plupart des applications, après une évaluation des risques, cette fonction de sécurité permet au robot de fonctionner sans avoir besoin de protection de sécurité.
Évitez les travaux pénibles
Chez la société scandinave de tabac, les robots collaboratifs peuvent désormais travailler directement aux côtés d'employés humains pour boucher les canettes de tabac sur les appareils d'emballage du tabac.

Chez Scandinave Tobacco, le robot UR5 charge désormais les canettes de tabac, libérant ainsi les salariés des corvées répétitives et les transférant vers des tâches plus légères.Les nouveaux produits de bras mécaniques de la société Youao Robot sont bien accueillis par tout le monde.
Les nouveaux robots peuvent remplacer les travailleurs humains dans des tâches lourdes et répétitives, libérant ainsi un ou deux travailleurs qui devaient auparavant effectuer le travail à la main.Ces employés ont maintenant été réaffectés à d'autres postes dans l'usine.Puisqu’il n’y a pas assez de place sur l’unité de conditionnement en usine pour isoler les robots, le déploiement de robots collaboratifs simplifie grandement l’installation et réduit les coûts.
Le tabac scandinave a développé son propre luminaire et a demandé à des techniciens internes de réaliser la programmation initiale.Cela protège le savoir-faire de l'entreprise, garantit une productivité élevée et évite les arrêts de production, ainsi que le recours à des consultants d'externalisation coûteux en cas de panne d'une solution d'automatisation.La réalisation d’une production optimisée a conduit les chefs d’entreprise à décider de maintenir la production dans les pays scandinaves où les salaires sont élevés.Les nouveaux robots du cigarettier ont une période de retour sur investissement de 330 jours.
De 45 bouteilles par minute à 70 bouteilles par minute
Les grands constructeurs pourraient également bénéficier de nouveaux robots.Dans une usine Johnson & Johnson à Athènes, en Grèce, des robots collaboratifs ont considérablement optimisé le processus d'emballage des produits de soins capillaires et cutanés.Travaillant 24 heures sur 24, le bras robotique peut prélever trois bouteilles de produit sur la ligne de production en même temps toutes les 2,5 secondes, les orienter et les placer à l'intérieur de la machine de conditionnement.Le traitement manuel peut atteindre 45 bouteilles par minute, contre 70 produits par minute avec une production assistée par robot.
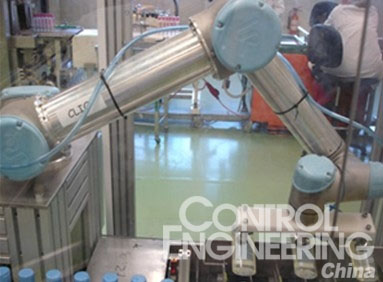
Chez Johnson & Johnson, les employés aiment tellement travailler avec leurs nouveaux collègues robots collaboratifs qu'ils ont un nom pour cela.UR5 est désormais affectueusement surnommée « Cleo ».
Les bouteilles sont aspirées et transférées en toute sécurité, sans risque de rayure ni de glissement.La dextérité du robot est cruciale car les bouteilles sont de toutes formes et de toutes tailles et les étiquettes ne sont pas imprimées sur la même face de tous les produits, ce qui signifie que le robot doit pouvoir saisir le produit aussi bien par le côté droit que par le côté gauche.
N'importe quel employé de J&J peut reprogrammer les robots pour effectuer de nouvelles tâches, ce qui permet à l'entreprise d'économiser le coût de l'embauche de programmeurs externalisés.
Une nouvelle direction dans le développement de la robotique
Ce sont là quelques exemples de la manière dont une nouvelle génération de robots a réussi à relever des défis du monde réel que les robots traditionnels n’avaient pas réussi à résoudre dans le passé.Lorsqu'il s'agit de flexibilité de la collaboration humaine et de la production, les capacités des robots industriels traditionnels doivent être améliorées à presque tous les niveaux : de l'installation fixe à la délocalisation, des tâches périodiquement répétitives aux tâches fréquemment changeantes, des connexions intermittentes aux connexions continues, de l'absence d'intervention humaine. de l'interaction à la collaboration fréquente avec les travailleurs, de l'isolement de l'espace au partage de l'espace, et des années de rentabilité au retour sur investissement quasi immédiat.Dans un avenir proche, de nombreux nouveaux développements se produiront dans le domaine émergent de la robotique, qui modifieront constamment notre façon de travailler et d’interagir avec la technologie.
Le tabac scandinave a développé son propre luminaire et a demandé à des techniciens internes de réaliser la programmation initiale.Cela protège le savoir-faire de l'entreprise, garantit une productivité élevée et évite les arrêts de production, ainsi que le recours à des consultants d'externalisation coûteux en cas de panne d'une solution d'automatisation.La réalisation d’une production optimisée a conduit les chefs d’entreprise à décider de maintenir la production dans les pays scandinaves où les salaires sont élevés.Les nouveaux robots du cigarettier ont une période de retour sur investissement de 330 jours.
De 45 bouteilles par minute à 70 bouteilles par minute
Les grands constructeurs pourraient également bénéficier de nouveaux robots.Dans une usine Johnson & Johnson à Athènes, en Grèce, des robots collaboratifs ont considérablement optimisé le processus d'emballage des produits de soins capillaires et cutanés.Travaillant 24 heures sur 24, le bras robotique peut prélever trois bouteilles de produit sur la ligne de production en même temps toutes les 2,5 secondes, les orienter et les placer à l'intérieur de la machine de conditionnement.Le traitement manuel peut atteindre 45 bouteilles par minute, contre 70 produits par minute avec une production assistée par robot.
Heure de publication : 25 avril 2022